All in pill and capsule forming machines
Comprehensive Solutions in Pill and Capsule Forming Machines
Leaders in Advanced Solutions for Machinery in the Pharmaceutical Sector
Our equipment is characterized by its exceptional quality and operational simplicity, offering a wide range of solutions for the production of tablets. Among our catalogue, powder mixers stand out, designed to guarantee perfect homogenization of the ingredients. We also have tablet forming machines through tablet presses, which ensure precision and uniformity in each unit produced. For the encapsulation process, our machines automatic capsule filling machines They offer optimum and efficient performance. In addition, we have pill counters and automated systems for blister formation and filling, which optimize both time and resources, increasing productivity and efficiency in the production line.
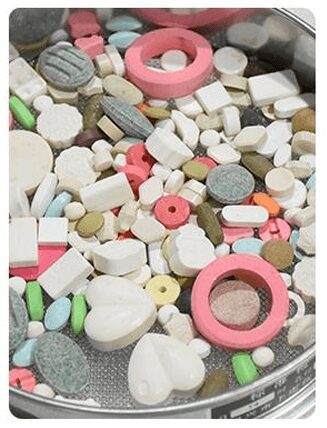
Pill making machines
Tablet forming machines of different shapes presses
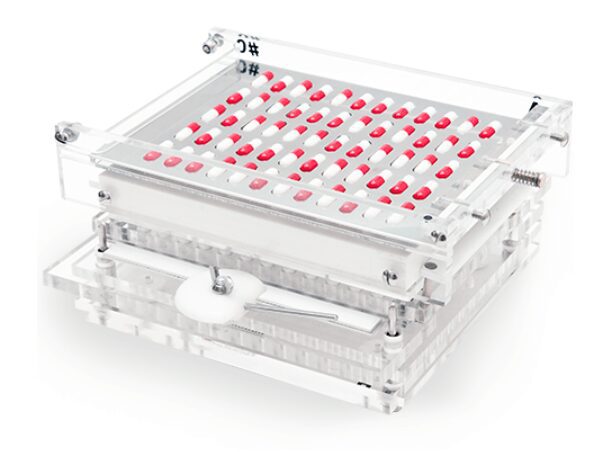
Encapsulating machines
Machines for making tablets in gelatin capsules 00, 0, 1, 2, 3, 4, 5.
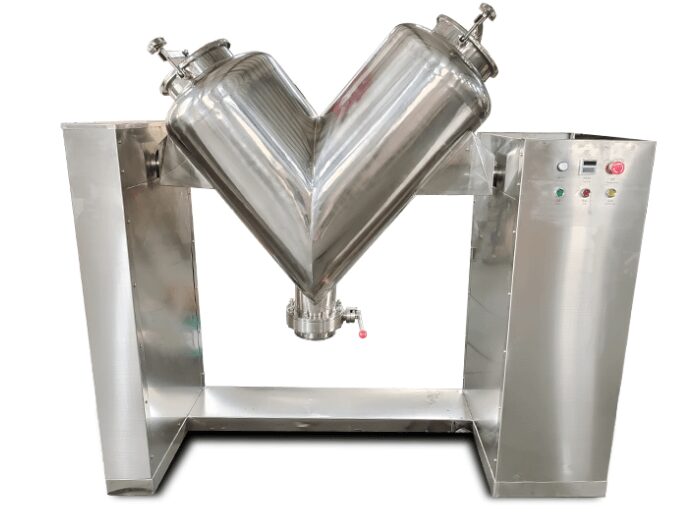
Powder mixers
V-shaped, horizontal and vertical powder mixing machines
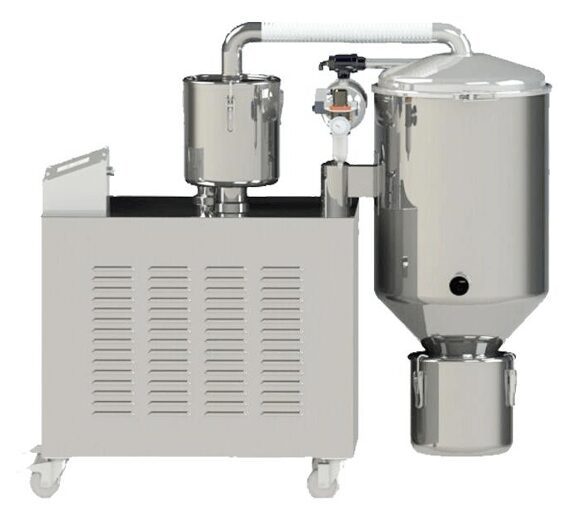
Powder feeders
These machines are responsible for moving the dust by vacuum.
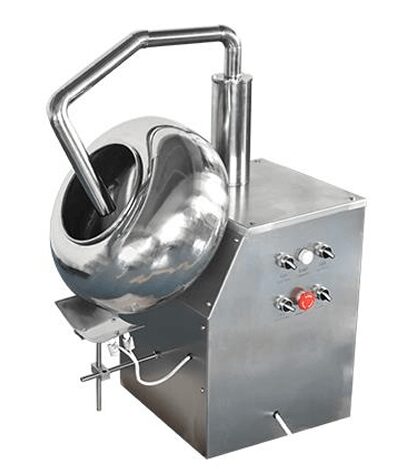
Coating drums
Mixing machines for coating capsules for a homogeneous dust-free finish
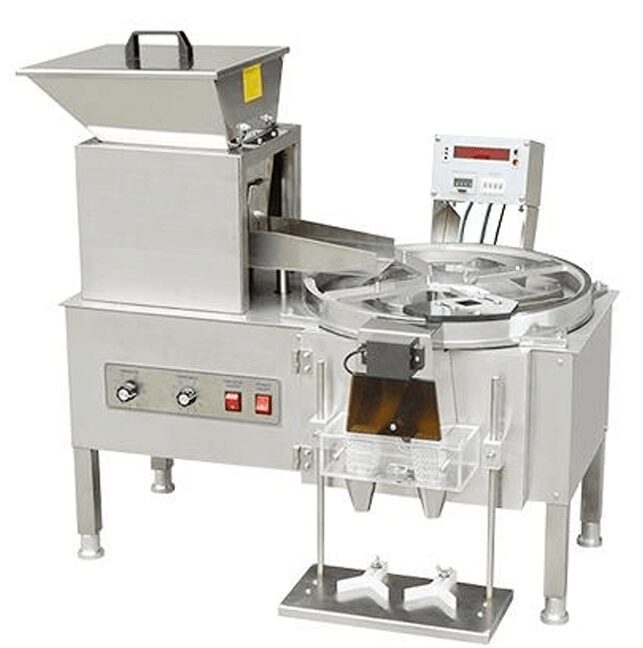
Pill counters
Machines in charge of counting and filling pill bottles
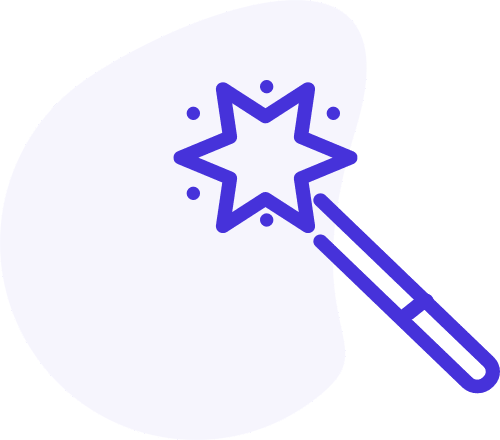
Packaging
Machines for packaging pills and capsules in individual blister packs
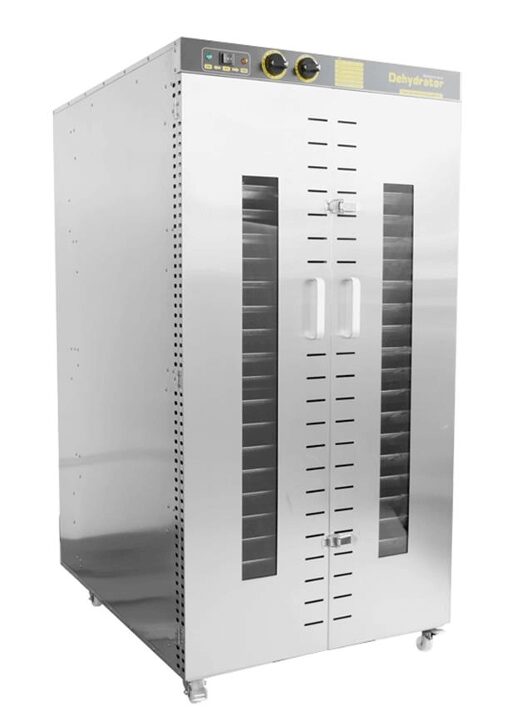
tablet dryers
Machines responsible for drying tablets to remove moisture residues

Dust cleaners
Machines for cleaning powder residues from pills and capsules
Why Choose ARC Distribution for your Pharmaceutical Machinery Solutions?
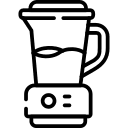
Cutting-edge Guarantee
At ARC Distribution, we are not only dedicated to providing the highest quality machinery for pill production, but we back each piece of equipment with an exceptional 2-year warranty. Our products are the result of meticulous attention to detail and the highest manufacturing standards, ensuring unmatched performance and long-term reliability for your pharmaceutical operations.
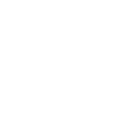
Recognized Experience
With more than a decade of experience in the sector, ARC is positioned as a leader in the field of professional and industrial machinery, extending its expertise to the pharmaceutical sector. Our track record is synonymous with innovation, quality and a deep commitment to the needs of our customers, providing solutions that not only satisfy, but exceed expectations in pharmaceutical production.
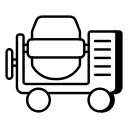
Expert Support All Year Round
We understand that the operation of specialized machinery, such as that needed for the manufacture of tablets and capsules, requires constant technical support and advice. That is why, at ARC Distribution, we are proud to offer a comprehensive advisory service available 365 days a year. Our team of experts is always ready to resolve any questions or needs that may arise, ensuring that your production never stops due to a lack of technical support.
We Have Great Answers
Frequently Asked Questions
How to Choose Your Right Pill Forming Machine?
To select the tablet forming machine In order to find the right equipment, it is crucial to consider several key aspects that will ensure that the equipment meets your specific production requirements. Firstly, it is important to identify the type of product to be processed, differentiating whether this is a dust or if it has a denser consistency with a certain degree of humidityThis distinction is vital, as it will determine the compatibility of the material with the type of machine and its compression or molding mechanism.
Additionally, the desired production capacity is another determining factor. Evaluating the amount of pellets you need to produce in a specific period will help you choose a model that not only suits your current needs but also has the potential to accommodate future production expansions.
Finally, consider the size and shape of the capsule or tablet to be produced. Depending on the specifications of the final product, some machines offer greater versatility and adaptability in terms of available sizes and shapes.
Taking these essential aspects into account will guide you towards choosing a tablet press that not only aligns with your production needs but also ensures efficiency and quality in your pharmaceutical product line.
How to Select the Right Powder Mixing Machine?
When looking for the ideal machine to mix the powder components of your tablets, it is essential to consider several key factors to ensure that the equipment is perfectly suited to your production requirements. First and foremost, the total number of kilograms to be mixed in each batch is a crucial criterion. This capacity will determine which mixer model is best suited to your operations, thus ensuring optimal production.
Our mixers are available in three distinct models, each with different capacities and specific configurations to suit a variety of production needs. V-shaped models are ideal for homogeneous mixing of powder components, while vertical models excel in limited spaces and horizontal models are preferred for their flexibility in handling different types of mixtures and volumes.
Choosing the right model will directly depend on the specific characteristics of the products to be mixed and your production objectives. Considering these aspects will allow you to select a powder mixing machine that not only meets your quality and efficiency expectations but also contributes to the success and scalability of your production process.
How to Choose the Perfect Encapsulation Machine for Your Production?
Select the right machine automatic capsule filling machine either manuals to make capsules is a process that requires a detailed analysis of your specific production needs. A crucial factor to consider is the type and size of capsules you plan to fill. Standard sizes available include 00, 0, 1, 2, 3, 4, and 5, each suitable for different volumes and types of products.
Another essential aspect is determining the required production capacity. Knowing the number of capsules you need to produce per hour or per day will help you decide between the options manual, semi-automatic machines and fully automated. This decision is critical, as the level of automation must align with your production goals to ensure efficiency and effectiveness.
The Manual machines are ideal for smaller productions or for companies that are starting out and want to keep investment costs low. Semi-automatic machines offer a balance between manual control and automation, suitable for intermediate production volumes. On the other hand, fully automated machines They are perfect for high production volumes, where efficiency and speed are critical to meet market demands.
Choosing the right machine involves weighing these factors carefully to find the equipment that not only meets your current production requirements, but also has the ability to adapt to the future growth of your business.
When is it Necessary to Incorporate a Tablet Dust Cleaner into Your Production Process?
The use of a tablet dust cleaner becomes essential in any capsule and pressed tablet manufacturing process to ensure the quality and integrity of the final product. During the production of tablets, it is common for residue and dust to be generated which can adhere to the surface of the capsules or tablets. This residue not only affects the appearance of the final product, but can also compromise its quality and accuracy in terms of dosing.
The addition of a powder cleaner is designed to effectively address this issue. Compatible with both capsules and pressed tablets, these machines use advanced vacuum aspiration systems to remove residual powder. This process not only cleans the final product, but also allows the powder to be recovered for reuse by pressing it again, thereby maximizing the efficiency of the material.
Using a powder cleaner is crucial to maintaining hygiene and quality standards in pharmaceutical production. By removing residual powder, cross-contamination is prevented, dosage consistency is ensured, and product presentation is improved. This additional step in the production process reflects a commitment to excellence and product safety, which are fundamental aspects in the pharmaceutical industry.
When is it Essential to Have a Pill or Capsule Counting Machine?
The implementation of a pill or capsule counting machine becomes an indispensable requirement after the tablet or capsule production process. This need arises in the packaging and dosing phase, where it is crucial to ensure an accurate number of units per package, whether jars or boxes, typically in batches of 30 units or any other specific quantity required.
The main advantage of using these machines is the elimination of manual counting, a process that is not only time-consuming but also subject to human error. Depending on your production needs and the scale of your operation, you can opt for semi-automatic or fully automated solutions. Semi-automatic machines are suitable for smaller productions or for companies looking for flexibility with a lower initial investment. On the other hand, fully automated machines are designed to handle high production volumes, optimizing efficiency and accuracy in counting and packaging capsules or tablets per hour.
Incorporating a counting machine into your production line not only ensures packaging accuracy, but also significantly improves process efficiency, allowing you to meet market demands more effectively and with consistently high quality standards.
What is a Vacuum Powder Feeder?
The vacuum powder feeder is an innovative solution indispensable for the efficient handling of powdered raw materials within production facilities. This system is crucial when the raw material is stored in one section of the plant and needs to be moved to another area for processing, encapsulation or compression.
Operating via a specialized pump, the vacuum powder feeder transports the product using a piping system to the main machine or tank. This vacuum conveying method not only minimizes manual contact with the raw material, ensuring a more hygienic and contamination-free environment, but also optimizes the efficiency of the transfer process.
The implementation of a vacuum powder feeder is essential for any operation that requires the safe and effective movement of powdered products throughout the production plant. By eliminating the need for traditional manual or mechanical transfer, this system provides a cleaner, faster and more efficient solution, ensuring that raw materials arrive at their destination in the best possible condition for further processing.
What Does Blister Packaging of Pills Involve?
The blister packaging process is carried out by a specialized machine that uses two rollers to form the blister, which is the transparent plastic part intended to house the capsules or pills. This machine is designed to accurately place each capsule within its respective compartment in the blister, following the specifications of the mold used.
Once the capsules or tablets are correctly positioned, the machine proceeds to seal the blister with an aluminium foil, ensuring the integrity and protection of the product. Finally, each blister is cut to the indicated size, preparing them for distribution or sale.
Furthermore, this technology is not limited to packaging solid tablets; it is also equipped to handle vials with liquids. Thanks to the versatility of the moulds included in the machine, it is possible to form blisters in various shapes and sizes, adapting to the specific needs of each product.
This packaging method not only offers optimal protection against moisture, air and other external factors, but also facilitates the safe dosing and use of medicines by consumers, standing out for its effectiveness and precision in the pharmaceutical sector.
Is a Crusher or Sieve Necessary Before Mixing the Components?
Uniformity in particle size of the powdered components is crucial to ensure the quality and appearance of pressed tablets. This is where crushers and sifters come into play, essential tools in the process of preparing the components before mixing. These machines ensure that all powdered components pass through a 120-point-per-inch mesh (or any other required specification), thus achieving uniform consistency in particle size.
This homogeneity is essential, since differences in grain size can negatively affect the final appearance of the tablet, manifesting in visible irregularities and affecting the perception of quality. Some components may have naturally different particle sizes, which without an adequate grinding and sifting process, could result in an uneven distribution within the pressed tablet.
Therefore, the implementation of a crusher or sieve before the mixing process not only improves the aesthetics of the tablets but also contributes to the uniformity in their composition and dissolution, factors that are essential to maintain the quality and efficacy standards of the final product.
Our Clients
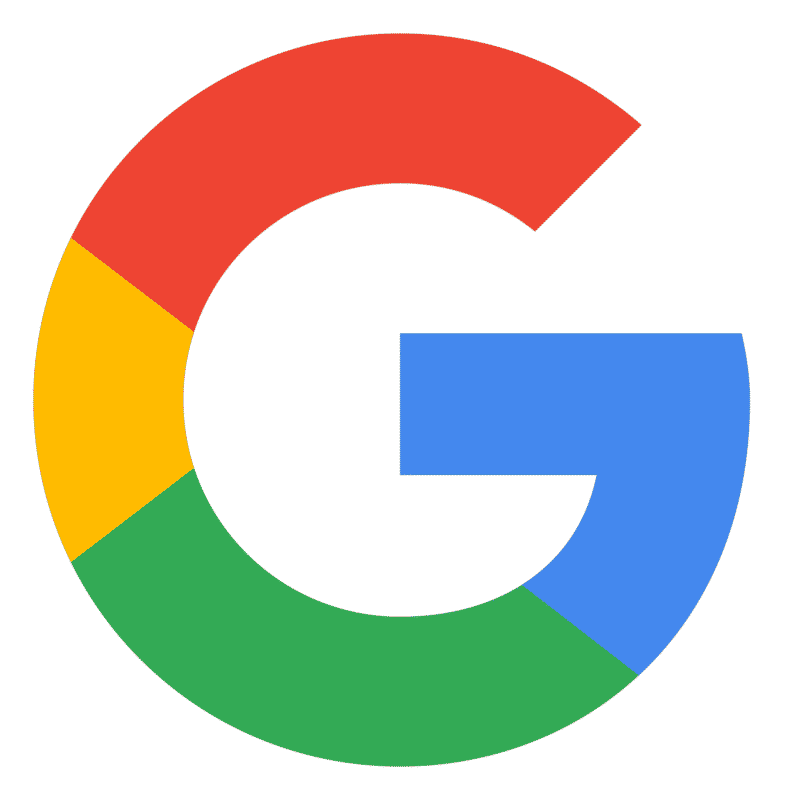
"Lamar Laboratories is extremely pleased with the purchase of a tableting machine from ARC Distribution. This equipment has greatly improved our production through its quality, efficiency and ease of use. The attention and technical support from ARC has been outstanding, ensuring that we made the right decision for our growth. We highly recommend ARC Distribution for their advanced solutions and excellent customer service in the pharmaceutical industry."
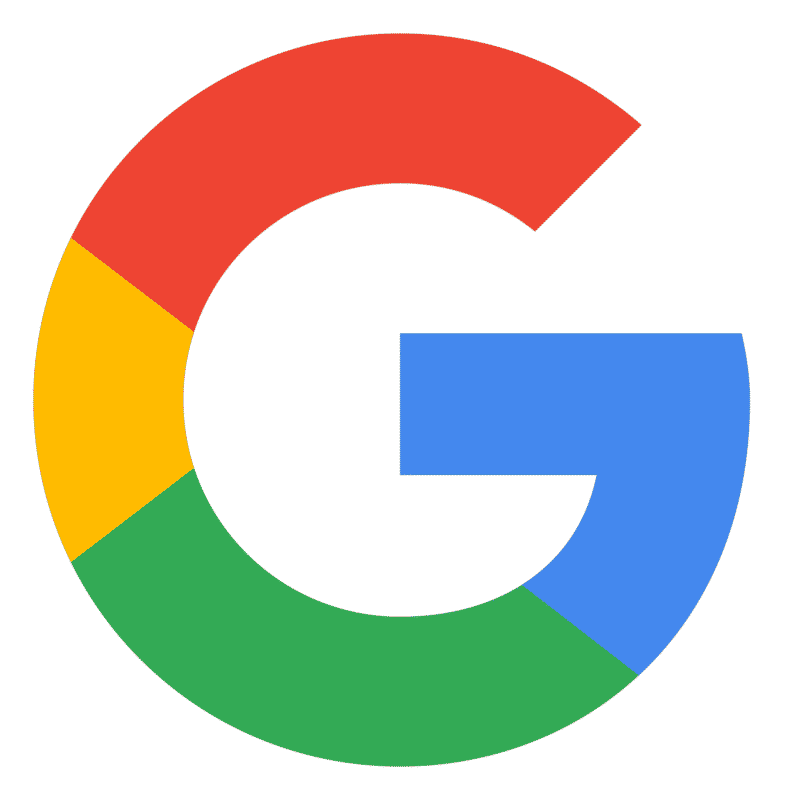
"PharmaTech Solutions has seen a significant improvement in the mixing of capsule components thanks to the powder mixing machine purchased from ARC Distribution. The accuracy, efficiency and ease of operation of this machine have been crucial in optimizing our production processes. ARC's customer service and technical support have exceeded our expectations, reinforcing our confidence in their technology. We highly recommend ARC Distribution for their innovative solutions and exceptional support in the pharmaceutical sector."
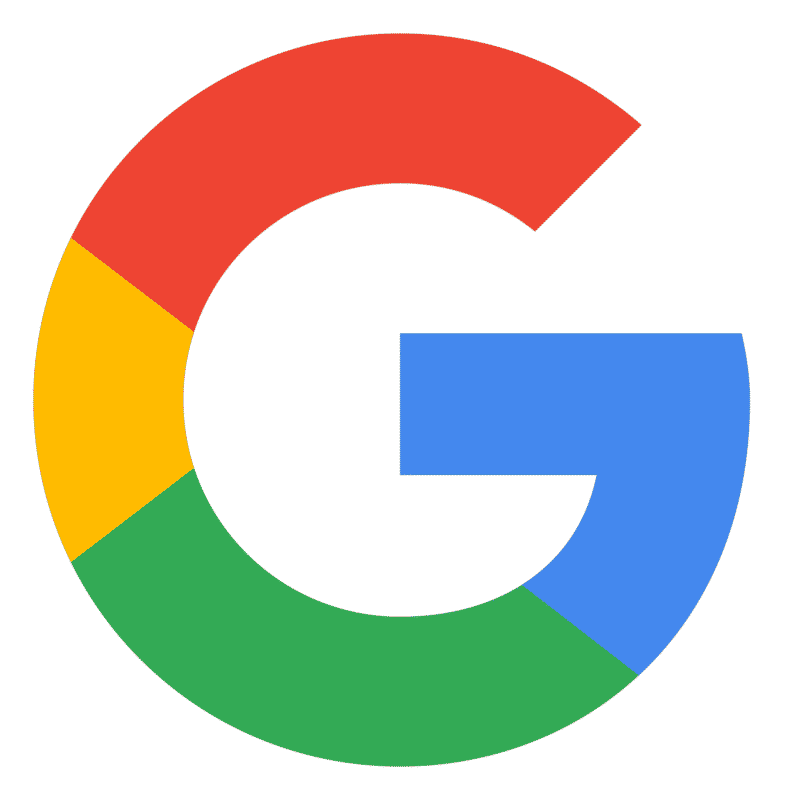
"Innovaciones BioFarm has seen a significant change in the efficiency of our packaging line after incorporating the automatic blister forming and filling machine from ARC Distribution. The speed, precision and reliability of the equipment have allowed a substantial improvement in our production capacity, while maintaining the highest quality standards. The purchasing experience has been excellent, highlighting the personalized advice and technical support offered by ARC. This acquisition has been a step forward in our quest for operational excellence, and we recommend ARC Distribution to those in the pharmaceutical sector looking for innovation and efficiency."
Committed to the Total Satisfaction of Our Clients
Your Journey to Innovative Solutions Starts Here!
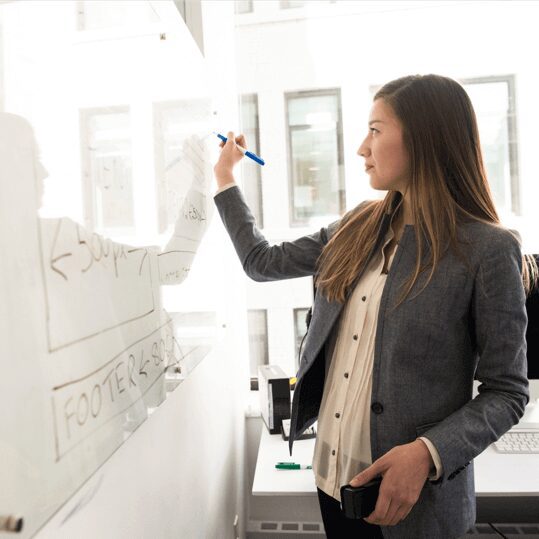